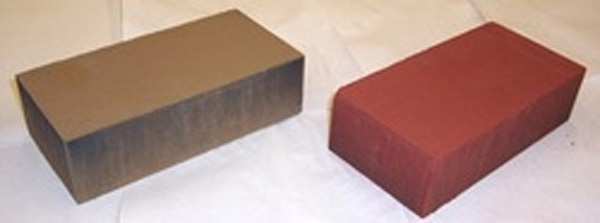
Yesterday’s blog post was about making bricks with rice hull ash. Today we’ll review a few benefits of using rice hull ash in non-Portland cement products such as bricks and geopolymer, and give a formula for making rice hull ash bricks with no cement. Please note how other agro wastes such as sugar cane ash peanut shell ash and coconut ash could also be used. Use what is low cost and locally available.
– Rice hull ash, which is extremely high in silica, improves workability, strength and impermeability of concrete mixes, while making the concrete durable to chemical attacks, abrasion and reinforcement corrosion, increasing the compressive strength by 10% – 20%.
– Bricks can be made with 100% fly ash at room temperature at lower cost than traditional clay bricks – see the “Greenest Brick”. (Note: their website is several years out of date and I can’t find any recent news on their product.)
– Products made of fly ash and rice hull ash are typically lower cost than Portland cement.
– Rice hull ash bricks are highly insulating and often used in refractories.
– Optional additive: Air entrainment additives create tiny air spaces in concrete and geopolymer to reduce weight, increase insulation value and resist damage from freezing. Larger, lighterweight bricks made with air entrainment additives would speed construction because workers wouldn’t have to handle as many bricks.
– Pozzolanas have been used in concrete since the ancient Romans developed Roman concrete (more durable than modern concrete). Pozzolanas can be used in combination with lime and/or ordinary Portland cement (OPC). When mixed with lime, pozzolanas will greatly improve the properties of lime-based mortars, concretes and renders for use in a wide range of building applications…rice hulls have been identified as having the greatest potential as it is widely available and, on burning, produces a relatively large proportion of ash, which contains around 90% silica.
– To produce the best pozzolanas, the burning of the hulls must be carefully controlled to keep the temperature below 700°C and to ensure that the creation of carbon is kept to a minimum by supplying an adequate quantity of air. At burning temperatures below 700°C an ash rich in amorphous silica is formed which is highly reactive. Temperatures above 700°C produce a crystalline silica which is far less reactive. The second step in processing is grinding the RHA to a fine powder, and ball or hammer mills are usually used for this purpose.
– Ultra-fine ash allows for a lower water-cement ratio and stronger concrete, additional resistance against early age stress development and restraint cracking, and decrease in permeability. (This is a very fascinating process. Scientists have developed a durable, rapid set, super high strength concrete using ultra-fine ash that’s ideal for bridges and similar high value structures.)
– The pozzolana must be blended with lime (Type-S) and/or OPC to produce a pozzolanic cement. This can be accomplished by human or animal-powered methods but full homogeneity is unlikely to be achieved and the strength and consistency of cements blended in this manner will be variable. Mechanical techniques, preferably intergrinding in a ball mill or, as a second option, dry blending in a pan or concrete mixer, will give better results in terms of both strength and consistency. With lime pozzolana cements, mixtures of 1:1 to 1:4 lime: pozzolana) by weight are used. A small percentage (normally 5-10%) addition of OPC will improve strength and decrease setting times.
– Another recipe: lime, sand and fly ash or rice hull ash (I wrote it down the other day but now can’t find the source for further details).
– Google Books: search Sustainable Building – Design Manual: sustainable building design practices for keywords lime, sand and ash. Their formula uses 30% rice hull ash plus red or black soil. The bricks are fired at 1,000 degree C.
– Other formulas use additives such as stone dust and gypsum.
– Alternative: Some add 20% rice hull ash to Portland cement to reduce costs.
Pozzolanas – Rice Husk Ash (RHA) and Pulverised Fuel Ash (PFA) – Technical Brief
Geopolymer Blog
Color chart of iron oxide pigments http://tondro.com/BlogImages/Pigments1.jpg
Image source: Make
Suggest the additive so that bricks look like clay bricks.
i want to learnt and give me short course .
I have no further information than that shown in this post and the previous one.
Interesting in rice husk ash brick making
Nice topic and nice flow of thoughts. I wasn’t aware of something like this, while going through new things I found this very interesting piece to read. Informative and interesting.
You can also blend it with ground granulated blast furnace slag in a strongly alkaline solution to form a geopolymer. If you know a little chemistry, track some of Joseph Davidovits work, he literally wrote the textbook on the stuff.
Take a look at my Geopolymer Houses blog. Davidovits’ video is what got me intrigued about using geopolymer and convinced me to do the blog. http://geopolymerhouses.wordpress.com/