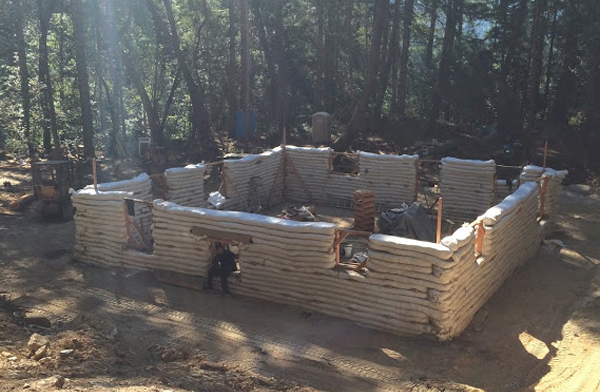
“UEB’s first 1,225sqft structure built with the semi-automatic 3d printer, the Earth Home Builder. 9 days of bag laying of 21″ bag. Fastest layer of 40′ length was laid in 11m16s! The crew was trained on site and ranged from ages 9 to 50+! Even with mechanization, anyone can still be a part!
Over the past 39 days United Earth Builders has been working to construct earthbag walls using the Earth Home Builder (EHB) on a 1225sqft earthbag home on the Yurok Indian Reservation in Northern California. This project was as back woods and rustic as one could get. All of the road base was donated by the Roads Department (135 tons) and the lumber that we needed for the project was taken from the timber felled months before. The tribe itself assisted in the acquisition of the main EHB skid steer the loader was borrowed from a local friend. We began by digging out the side of a large hill in order to clear and compact a pad leaving enough room for the EHB to easily maneuver. We were left with a clear pad and trench, carpentry and metals station, lumber mill station (Alaska Mark III and mini mill) I wish we had a Lucas, and our bagging station. We also had 135 tons or 10 trucks worth of road base!
The layout of the structure was as simple as could be. Thirty-eight foot lengths of foundation in a square. We would have liked to do a full 152’ footprint length but the EHB cannot hold more than 90’ on the sock holder so we went with four 38’ lengths on four runs. One unfortunate mistake that I had made was using 21” bag. I was hoping to use the smallest bag possible on the EHB to save on material but had not tested it until now. It was a tight fit and difficult to smoothly slide off of the sock holder even when full of earth. On the previous prototype we used a 24” bag which worked perfectly and we will continue to do so in the future. In order to fight against the snagging bag, the bag spotter (person making sure the bag is on the wall and straight) had to pull the tensioner from time to time and I had taken a metal grinder to the 90 degree cone to shave down some of the pointed edges and round it out a bit. Problem solved-ish.
Ahead of the EHB, we pre-cut the next bag in order to keep production moving after each bag is laid. The second skid steer is the loader that fills the EHB. Each hopperfull can lay about 20-30 feet of bag so our EHB needed to reload during bag laying. This can be tricky but with a good operator can take no time at all. We also had to take into account tipping. A heavy load can tip the EHB easily especially if there is no weight to counterbalance the skid steer. We used a 500lb cut log with some chain. WAY CHEAPER than renting an actual kit. The first 38’ run took about 47 minutes including the instruction.
After the bag was laid, the EHB driver loaded the next bag onto the sock-holder and awaited another load to go. A tamper team followed up behind us and double checked the spotters’ work on keeping the bag plumb to the string guides. Once the bag was adjusted properly in the trench we used a plate compactor to tamp the bags down to maximum compaction. Another issue was that the plate compactor we had was not the best. I am thinking that I am going to need two plate compactors to speed up the process for future projects. When factoring in the compaction, the first run took 1h23m to complete. Still way faster process than by hand, but if compaction holds up production it can make the EHB irrelevant. To combat the lagging compactor we added 2 people with hand tampers to pre-tamp before the compactor. We used the compactor to finish the compaction and that adjustment worked extremely well. No barbed wire was used in this structure nor any cement besides for the lintel and the bond beam. After compaction, we used #4 (1/2”) reinforcing bar to pin the layers of wall together every three layers. I wanted to create a, sort of, weave within the wall with the rebar so we cut the rebar at 2’ and staggered them each time they were inserted into the wall.
Once we completed the foundation, which was 2 layers at about 14” total depth, we set in the door bucks. Aside from the bag snags most of the bag laying from this point forward was smooth. At around the 6th layer we inserted ‘dead men’ [wood blocking] for the interior framing which will also allow the owner to install extra insulation or leave an open pocket of air in between the earthbag wall and wood interior paneling. In total we had three rows of the ‘dead men’ wall anchors and will have updates on how that worked out in future posts. We completed the bag work in 9 days with a group that had an age range from 9 to 50 years old. Despite being mechanized, this project still was able to integrate volunteers and peoples of all age ranges which is what I am most happy about.
All in all, the project is now on hold for cultural and salmon seasons that are in full swing but they should be back in full swing in spring and I will bring some updates as they come about.”
United Earth Builders
Photo gallery
Note: They’re using their new Earth Home Builder auger (automated system using a Bobcat) This project is a very good example of how this machine can be used. In this case there are minimal building codes, low cost materials and community contributions. Everyone could have safe, decent shelter with this mindset.
Woh’ Owen….that’s a LOT of rebar. The cost would send you to the poor house if I understand you correctly. I don’t get it???? Explain the layout for this. I’m confused.
Rebar is not particularly expensive. Weigh the cost of rebar against the cost of barbed wire, plus the time and labor involved. I’m just telling you my experience and that of others who have started using rebar pins and everyone so far feels it’s a better method.
Owen, question…..I went to the Photo Gallery to view their build and I was wondering what the 2×4’s between the rows on the wall was for? Is it to connect the rebar? Is this the way you do it as the wall gets taller? Do you just tie it together with wire or is there another method? Welding would melt the plastic. OR, am I completely wrong for the wood spacers use all together?? “IF” this IS what it’s for then how long should the rebar be to be efficient? They, I believe spaced the rebar every 3 foot. Am I correct on the spacing being 5 foot or is 3 foot correct? I appreciate your feedback because these are important questions regarding the use of rebar in my build. “Thank You My Friend”.
Builders insert wood blocking in adobe houses, earthbag, cob, etc. for later attachment of interior walls, shelving, cabinets, etc. Some call these gringo blocks.
Rebar pinning: 3′ spacing in tubing sounds good to me. With bags, one rebar pin per bag seems best, although it depends on the size and number of door and window openings, etc. The more openings (= weak areas) the more rebar you need.
Owen, what’s your opinion on the use of rebar pins staggered throughout the wall to create an interwoven pattern, like outlined in the article? Not necessarily in place of the barbed wire, but maybe in addition? Overkill??
I and others who have been doing this are very happy with the results. Richard at New Life (see previous posts) has decided to quit using barbed wire and just use internal rebar pinning. It’s quicker, easier and very strong. Barbed wire is dangerous and not fun to work with. Rebar pins next to doors and windows are particularly effective.
Reposted by James who is running the Yurok build:
“This such a great use for the USDA Rural Development Program! http://www.rurdev.usda.gov/Home.html
This is what I want to do with earthbag!
unitedearthbuilders.com