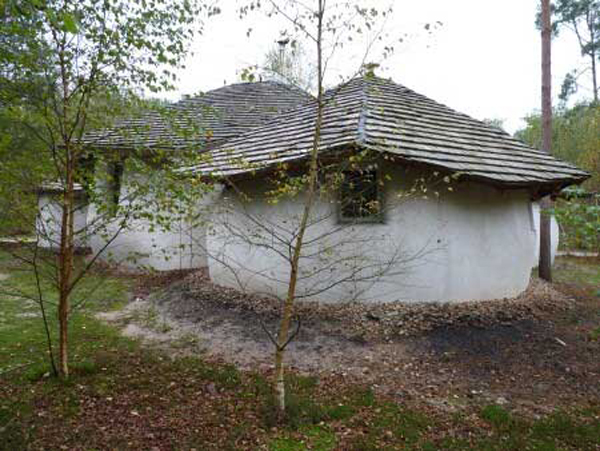
This fine looking home in France was built for a materials cost of only £2,500 ($3,800). This is one of the nicest homes we’ve profiled recently. Projects like this really keep me energized about natural building. Please forward to everyone you know and help this go viral.
Thanks to Jason for this great tip. He wants to build something similar in the UK. I suggested using strawbale roundhouses to speed construction and cut costs: pole frame construction using local wood, gravel bag foundation on rubble trench, straw bales stacked on top of gravel bags. This would avoid all the specialized dome work made with pallet wood.
Image source: Le Petit Casteropode
I love to make a stop by this website and have been for years. always a great read. Would a straw bale dome or roundhouse work with aircrete? Since its already insulated due to the air bubbles could it work to cover the entire bale section with the aircrete all over including the bottom? The bales would be sealed in by the aircrete. Just an idea. Aircrete can be done alone and is very affordable. It does seems past 4 inch thickness the price climbs but using the bales for its qualities covered with the aircrete could make it even cheaper. Have a small 3-4 inch layer covering everything. I first found out about aircrete from domegaia. I just always wondered what would be the cheapest option OF ALL the main uses like earthbag, aircrete, straw bale and more for a dome or roundouse. I seemed to always end back up to aircrete, straw bale and earthbag. A city lot can be had for $750 around here and i was just tossing ideas to one day build a cheap strong home between 4-800 sq ft. Maybe even smaller just to make it happen. again great website.
The “best” options depends on where you live — the climate, codes, available materials, etc. and your strength and skill level. Dirt cheap options like earthbags are my favorite, but are more laborious. Strawbale is great but not in rainy areas. Aircrete can be a good option but after additional research I’m see that it requires a good amount of research and testing. The best option for DIY aircrete is probably vertical walls on a small structure such as a roundhouse.
As always, start small to reduce risk and learn the necessary skills. Ex: plan the design so it can be built in stages.
Domes are best in deserts. That’s where they evolved from. Domes in rainy climates can turn black with mold over time.
Coming soon — another super dirt cheap option… Stay tuned. I have so much info it’s time consuming to figure how best to present it.
Midwest Ohio. Winters are cold but not as much snow in the Dayton / Cincinnati area these days. Spring is rainy but spotted showers usually. Summer produces the high humidity mid to late. Warm weather can extend into late september sometimes. Winter kicks in usually sometime in November if not the end of October or maybe a delayed winter mid to late December with 55 degree weather. Some lots that are available are square but most are narrow lots that are long and range usually about 3500 to a little over 5000 square feet. A roundhouse also sounds like a great idea as you stated with speed and ease of construction and I’m sure they can be just as secure as domes. Thanks again for all the inspiring information.
For that situation I would recommend strawbale walls with wide roof overhang to make sure the walls stay dry. This could include a wrap around porch on the side(s) of prevalent storms.
Check your code requirements before going too far. You can get SB approved but there are lots of requirements such as minimum square footage of rooms and over all house size and set backs that have to be met.
Greetings,
Wow this is wonderful. I am a Sister with the Ethiopian Orthodox Church in America and am seriously thinking about building our hermitage/monastery by these methods. This home in France just boost my confidence that we can really achieve this goal.We are new to cob and straw bale building. Would this type of building hold up in Up State New York or in other places in the Northeast/central of America?
God Bless You
Sister Ivory
Yes, there are lots of strawbale buildings in cold climates. There are strawbale and natural building organizations in numerous places, including your area. Look up Natural Builders Northeast at http://www.nbne.org/
And as I said previously, I would build roundhouses instead of domes for speed and ease of construction.
Cob is super slow and best used for small projects.
Thanks. As a matter of fact, we have contacted them already and found them to be a wonderful resource. Thanks for the conformation.
Sister Ivory
Here is a link about decay resistance of untreated wood species in the USA with two very different climates. Wisconsin and Mississippi.
http://www.fpl.fs.fed.us/documnts/pdf1995/highl95a.pdf
Thanks for the link! I didn’t think to look up the durability of hardwoods online. White oak and red oak both of durabilities of over 20 years! That means no stain or other finish is required. So using pallet wood shingles is a viable and practical possibility I’ve never heard of. Great news. This is good enough for a separate blog post. Thanks again.
Here are some embedable videos, if you want them.
http://www.youtube.com/watch?v=feE1cIQ-kbo
http://www.youtube.com/watch?v=5Mmv8qYsYp4
http://www.youtube.com/watch?v=BuzgHCrmpL0
The second video listed above appears to be the same video you posted, but with a music soundtrack.
Note the unplastered exposed bale exterior wall at the 1:55 mark, the 3:50 mark, and the 5:00 mark of the third video. I wouldn’t recommend that technique to others for a long lasting structure, but perhaps the structure wasn’t completed yet when that portion of the video was shot. Hopefully those areas got plastered. As they are shown in the video they are serious holes exposing bales to any wind driven rain. Leaving exterior bales unplastered like that is asking for mold and straw decomposition problems. It would have made a lot more sense to plaster the entire surface of the domes with at least a layer of earthen plaster before putting the roofs on top. Then a layer of stronger lime plaster over the exposed walls after the roof went on. I fear they will have problems with the areas of the building that have had exposed bales.
Note the empty glass bottles as foundation perimeter insulation (partially completed) at the 3min mark of the third video. Good idea. I had never considered attempting to insulate a foundation in that manner before, but it ought to do a decent job.
I’m particularly impressed with what appears to be an all pallet wood roof. Pallet wood roof frame, pallet wood slats, and it appears to be pallet wood shingles. It turned out very attractive. I’m not certain how long the life of a pallet shingle roof will be, but it certainly is an inexpensive option. It probably won’t last as long as cedar, or some naturally rot resistant wood shingle species, but for the price, it’s hard to beat using free pallets to build an entire roof.
All bales should be plastered as soon as possible to keep pests out. I’ve heard stories of mice getting inside walls and dying. The stench was so bad that the wall had to be torn apart to find the dead mouse. Also, sooner or later the roof will leak (they always do) and so you need to make sure water can’t get into the bales. It’s a big hassle to tear apart walls and replace rotten bales. The most common problem is water leaks at the base of windows. That’s why flush mounted/surface mounted windows and wide roof overhangs are recommended.
One big plus for building roundhouses instead of domes is the frame and roof can be built first. Vertical walls are far easier to build than domes. Add the bales later after you get the framing inspection (and rough plumbing and electrical inspections). Leaving bales exposed to the elements like in the video is just asking for trouble. One good rain would ruin the whole thing.
Also note, it’s interesting to know that building officials in the UK have no problems with accepting straw bale houses. Jason sent me two links to recent projects there. (There are many older projects, besides.) We don’t know of any code approved earthbag houses in the UK yet. Jason may use a rammed tire foundation since earthbag building hasn’t caught on there yet. (Gravel bags are faster and easier.)
I’ll throw in some additional thoughts.
The areas that are left unplastered are obviously areas that would be difficult to reach if attempting to plaster after the roof was put on.
As I stated earlier, in an idea scenario, the entire exterior surface of the domes should be plastered, at least with an earthen plaster, before the roofs are constructed. This would eliminate any problems with hard to reach areas.
Also important to note would be how critical it would be to use correct flashing at the intersection between the vertical(ish) dome wall, and the roof surface. Getting that one detail correct makes all the difference between a soggy wall that molds and rots away, and a wall that lasts for decades or even centuries. There are many excellent roofing websites and videos that describe the correct procedures for installing step flashing between a vertical wall and a roof. The flashing material itself need not be an expensive store bought product. There are multitudes of items that can get salvaged that could be turned into excellent, and often even superior pieces of step flashing. If you use pieces of scrap sheet steel to make your own step flashing, just make certain that it is protected from water, and rusting. Steel cans cut up is what most people might first think of for flashing material, and it would work, but I suggest looking for a heavier gauge (thicker) metal. I suggest cutting sections out of old scrap appliances. The outer covering of old water heaters for example. However, don’t be afraid to be creative and use whatever you can find locally for free. Once you have cut out all your pieces of (free) step flashing, go head and paint them, including all the cut edges and the area where crease where you will have needed to fold the metal and any existing paint will likely have cracked. Painting will dramatically slow or even stop the rusting process. It will save you many headaches in the future.
Thanks for the links, Jay. The third link shows a more thorough view of the nearly completed home. The outcome is very impressive! Hats off to the designer/builders. Yes, there are some unfinished surfaces, but they’re 99% done and it looks great.
Outstanding details include:
– pallet wood floors, cabinets, furniture, etc.
– gently curving walls and window openings create a very appealing, soothing feel
– artistically crafted skylight
– gutters hidden behind fascia boards, and gutters that direct water away from valleys
– roof modified for improved looks and function (ex: more light can enter windows)
If you’re thinking of building a home like this for under $4,000, then be sure to find an area with few or no codes. This would obviously never be permitted in areas with typical building codes.
And if you’re thinking of building and selling these for a living, be prepared for push back from the powers that be. Plan on lots of rats coming out of the woodwork to put a stop to your plans. Builders, realtors, building supply centers, government workers, bankers, etc. make millions off the current racket and they don’t want the party to end (for them). This is something I harp on constantly, but I’m just repeating it again for new readers. ***This project is proof positive we would not have a housing crisis (severe lack of affordable, quality housing) if people could build their own $4,000 houses!!!!!!
And since I’m a lifelong builder, I’d also like to add how I’d love to build houses similar to this (roundhouses versus domes). Imagine building something like this for a few thousand dollars, plus the cost of 2-3 laborers and selling them for $50,000 apiece. They’d sell like hot cakes. Even families with minimum wage jobs could afford the homes. You’d have unlimited demand. You could train 100 crews and never keep up.
Shingles: rot resistant woods such as cedar and redwood would last longer, like you say. But you can’t argue with the price of pallet shingles. Choose hardwoods such as oak (very common in US pallets) and apply 2-3 liberal coats of exterior stain before installing. Restain every 5 years or so as needed. Replace in 20-30 years if necessary with more free pallet wood. Enjoy laughing about all the money you’re saving. The added labor would be offset by free materials. Build small so the labor isn’t excessive.
No kidding.
Oh the horror! A 20 to 30 year roof?
You mean a roof that has the same life expectancy of the most common roofing material used in America today? Commercial Asphalt Shingles have about that same life expectancy.
I both agree and I disagree with your comment about staining the shingles.
The builder should think carefully about whether or not rain will be harvested from the roof, and how that harvested rain water might be used. If someone plans to use that rainwater for drinking purposes, it become critical that whatever stain or sealers used on the wood roof be safe for contact with your drinking water supply. Not all products on the market today would fall into that category.
Staining the shingles will certainly extend their life, but don’t be fooling about extending the life of your shingles at the cost of shortening your own.
For sure you wouldn’t want to drink the water. The current system shown in the video is drained away from the building. But as an afterthought, it would be better to use boiled linseed oil or something less toxic. How long would untreated oak last? Probably not very long in a rainy climate.
How long would untreated oak shingles last?
That’s going to be hard to pin down a number for.
There are hundreds of different varieties of oak species. They are not all the same. Many are more rot resistant than others. Combine that with the variability in different climates, and you might be better off trying to predict winning lottery numbers.
However, “shingle oak” is very common where I’m from. Some of the well built old oak roofs around here can last 50 years or more.
At the same time, there are also plenty of shoddily constructed oak roofs that don’t last 20 years.
Getting wood from pallets is pretty much going to be a roll of the dice about what specific species of wood one might get, even if you are skilled enough to identify which boards are oak and which ones are not.
Your 20-30 year guess for a pallet shingle roof seems reasonable. I would suggest that using long shingles, and only exposing a limited portion on each course would be the best technique to hedge one’s bets to get the longest life out of such a roof. Perhaps exposing a maximum 1/3rd or so of each shingle per course or less, 1/4th of each shingle exposed per course would be even better. That would mean that every square inch of any portion of the roof would have at least 3 layers of shingles on it providing triple redundancy. 4 layers of redundancy if only 1/4th of each shingle is exposed. Since the shingles themselves are essentially free someone can afford to use a lot more shingles on the roof than they otherwise might.(obviously your labor is the biggest expense).
Lloyd at Shelter Pubs has done a lot of work with wood shingles.
Here is his web page with his recommendations, but keep in mind that he mostly worked with splitting his own shakes from trees, and hasn’t done as much with pallet wood shingles.
http://www.shelterpub.com/_shelter/shelter_shakes.html
I suggest taking Lloyd’s recommendations, and adding extra margin for error since pallet wood is going to be inherently unpredictable.
Thanks Jay. Good input. Along with Michael’s suggestion (see his comment) I’d like to use your suggestions in a separate blog post. I can’t recall anyone using pallet shingles and so it would be great to blog about this possibility. Also, it would be good to get input from others who have used pallet shingles. Maybe the Paligloo builder could chime in.
Split wood — shingles split with the grain of the wood — is preferred. Pallets are made of sawn wood. That’s just one factor to consider. Another is nail holes and the spacing between nail holes. You’d want to trim one end to get rid of the holes. The distance to the next holes would be a factor in determining the overlap.
A nail gun would work best since the wood will be very hard and dry and prone to splitting.
A small jointer onsite or hand plane would be a plus since pallet wood is ripped at high speed and the edges tend to be very rough.
New readers: Our blog has extensive coverage of all ways of building with pallets — probably the best selection of info on the Internet today. Use the search engine on the right and search for pallets or pallet wood.
No problem, Owen. Use whatever you want.
As I was going about my day yesterday, my thoughts kept returning to pallet shingles, (my brain tends to do stuff like that a lot.)
The more I thought about it, the better I liked the idea, but the more I thought about it, the more important it seemed to me that installation techniques are more important than with many other roofing materials.
You mentioned a planer. I suggest a simple hand plane is more than sufficient. I’ve done some wood roofing, and a good roofing hatchet and a good (very sharp) block plane is about all that is normally needed. (Everyone should know how to sharpen their own hand plane blades properly. A sharp blade in a cheap plane is a far better tool than a dull blade in an expensive fancy plane.) There are a plethora of techniques an YouTube videos on this topic.
If using pallet shingles… I would add a drill and a saw to that list. My experiences working with pallet wood in other projects indicates to me the importance of predrilling holes before nailing pallet wood. It often splits so very easily. Where practical, many of the existing nail holes could probably get reused when nailing up the shingles, but you’ll still probably need to drill through all the underneath layers of shingles before hitting the strapping. Yes, pre-drilling will slow down the installation, but it will drastically reduce the number of split shingles, and produce a much better quality roof.
The saw will be needed, especially when ripping a pallet shingle lengthwise. Normal shingles are thin enough to split lengthwise with a roofing hatchet, or a utility knife. That’s not going to happen with the much thicker pallet shingle. You’ll definitely need a saw. That’s not to say that you’ll need to rip very many shingles, but it’s typical to need to rip one or two shingles per course, especially the last shingle installed in each course to get things to fit right. The new tiny battery operated circular saws they have on the market now might be the perfect tool that you could take up on the roof with you and just freehand the cuts. However, a simple handsaw could do the job very well also, and you never need worry about batteries going dead. Just keep it sharp. (Yes… I’m talking about everyone knowing how to sharpen their own handsaw. It’s an important skill that everyone working with tools should know how to do.)
I also recommend a hot dipped galvanized ring shanked or spiral shanked nail. It will need to be long enough to penetrate through all the layers of shingles that result from whatever exposure is chosen, and still have enough grab into the strapping to hold well.
It is always tempting to try to re-use the nails that came out of the pallets. In fact, I always keep a bucket of old used nails around, and use them in all kinds of projects. Nailing a roof up is a really bad place to re-use nails. You really want the rust protection on a roofing nail, and the nails typically used in pallets simply don’t have any.
You make an excellent point about nail holes. The spacing of those nail holes will be part of the equation that determines exposure per course. It will be best to make certain that the exposure for each course overlaps whatever nail holes are in the previous course.
“Roof Jacks” They are your friend. Get some or make some. Use them. Makes the job much safer, easier, faster.
Good points. Yes to having a hand plane (block plane) up on the roof. I was suggesting prejointing the edges on the ground. Run all the shingles over a little jointer or use a handheld electric jointer to clean up the edges.
Love the soundtrack on the 2nd link. I don’t know French. It sounds like he’s singing “I love to save money. Forget building codes. Build it yourself. I love to save money.” Anyway, he sure sounds happy.