My previous post described an alternative bond beam for curved walls; this post is on straight walls. Conventional reinforced concrete bond beams may not be affordable or the materials unavailable. Or maybe you want to reduce or avoid using cement. Here’s one low-tech, low-cost bond beam design. It’s even possible to use salvaged materials for all or most of this bond beam.
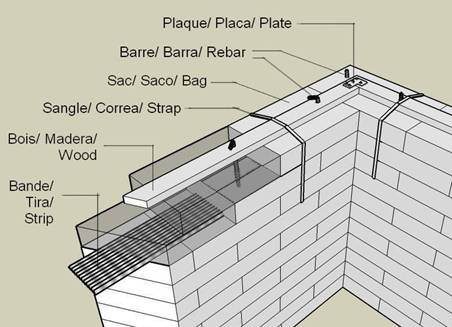
Materials: Corrugated metal roofing, 2×4 (5x10cm) wood, metal brackets/mending plates and screws, 16d nails, ½” rebar, and twine, rope or strapping.
In this design, corrugated metal and wood top plates are bound together with twine or strapping to stiffen tops of walls. Top plates, joined with metal plates, provide for easy attachment of trusses or rafters. Drill holes in top plates every 24” (60cm) for rebar pins.
Vertical rebar pins about 24” (60cm) long tie the bond beam into the wall below. Driving the rebar at alternating angles adds strength.
Use 8-12” (20-30cm) wide pieces of corrugated metal roofing overlapped at ends about 12” (30 cm) and nailed to the bag below at overlap points. Lay two courses of earth-filled bags above the corrugated metal strips.
Drawing credit to Patti Stouter.
Hi, I’m sorry if this is the wrong thread, not sure if it’s still active.
On your page about reinforced concrete bond beams, for the materials you mention sand and cement mortar but not gravel. Does this mean that you make the bond beam from cement mortar rather than concrete?
The article also mentions the importance of the correct amount of cement in the mix, what is the mix ratio for this bond beam if not using gravel.
Leaving out gravel would be great for me as it’s costly to transport to my location, however I’m not sure about a bond beam without gravel in the mix, I’d appreciate any advice.
Typically some gravel is mixed with sand and cement for concrete, and I expect that this is what was really meant in that previous article.
The walls would be about 16 feet at their longest, depth of soil 3 or 4 feet, could be increased on the north side.
The foundation will be tamped earth. Door openings would be standard, windows possibly smaller than standard.
This sounds unrelated, but would a living roof/walls be a solution to water protection in a very wet climate?
I’m not a fan of putting floors below grade. This often leads to moisture problems. Even deserts have heavy rains. Better to build on high ground and build soil around the structure (earth berming or sheltering).
Add a shear wall or buttressing for long walls.
Tamped earth foundations are not very reliable. Maybe if you stabilize the soil and use it for a small cabin, etc. it may be okay. Better to build on rubble trenches and fill lower earthbag courses with gravel.
Living roofs tend to be expensive and time consuming. Your roof has to hold up extra weight and so it costs more. It is rather difficult to waterproof. It takes a lot of maintenance or the roof will turn into a weed patch.
I am wondering, maybe this is the wrong thread for this question… But if building a straight walled home, instead of building supports on the outside of the walls like many designs I’ve seen, would it be possible to have the home built into the earth 4 to 5 feet? Or would this not be enough to support the pressure on the walls?
The structure I want to build would have a loft, so hopefully that wouldn’t add any extra pressure to the walls.
You have to take it case by case: How long are unsupported walls? Height of walls? Size and spacing of door and window openings? Depth of soil against the house? Concrete foundation and bond beam?
A loft won’t change much, although the framing can help stabilize walls.