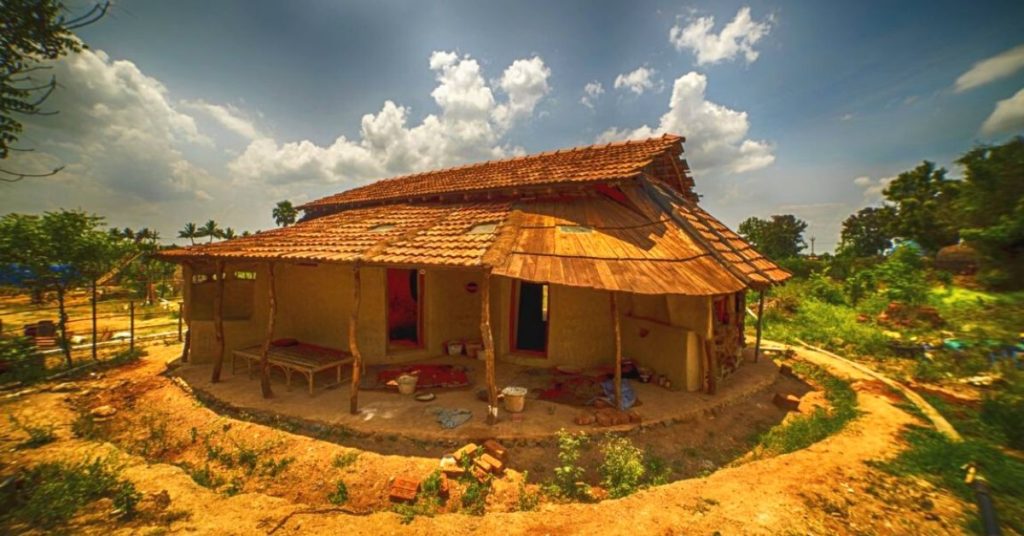
Over half of all homes in India are constructed of mud, and this is for economy as well as preference. Even in cities people are beginning to think that their grandparents had it right. Mud houses have several advantages over modern materials, and here are 7 reasons why they better:
1. Longevity
Mud brick can be a solid and durable construction material for walls and floors. It can last for centuries.
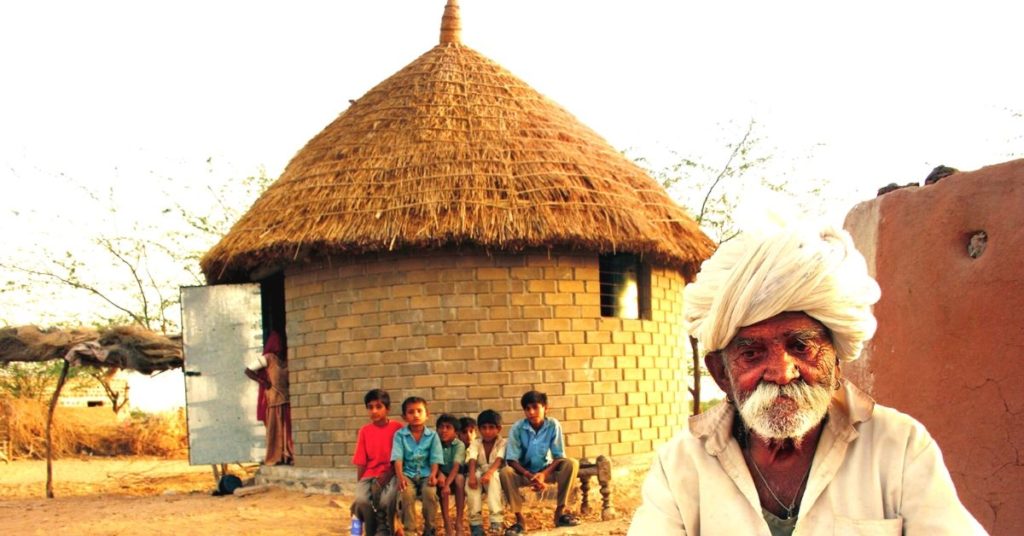
“While mud houses may cause some problems during rains, these issues can be addressed during the construction. Stabilisers like wheat husk, straw, lime, and cow dung can be used to prevent any damage,” Kerala-based architect Eugene Pandala explains.
For instance, using the Stabilised Compressed Interlocking Earth Block (SCEB) technology, local mud can be stabilised with five percent cement. The final compressed blocks have high structural strength and water-resistance. A prime example of this is Bhunga in Kutch, an earthquake-prone region, where houses are made with mud bricks, twigs and dung in a circular structure.
Likewise, in Rajasthan’s Barmer district, the houses have three vital elements–a cylindrical shape, mud, and thatched roofs.
2. Thermal mass
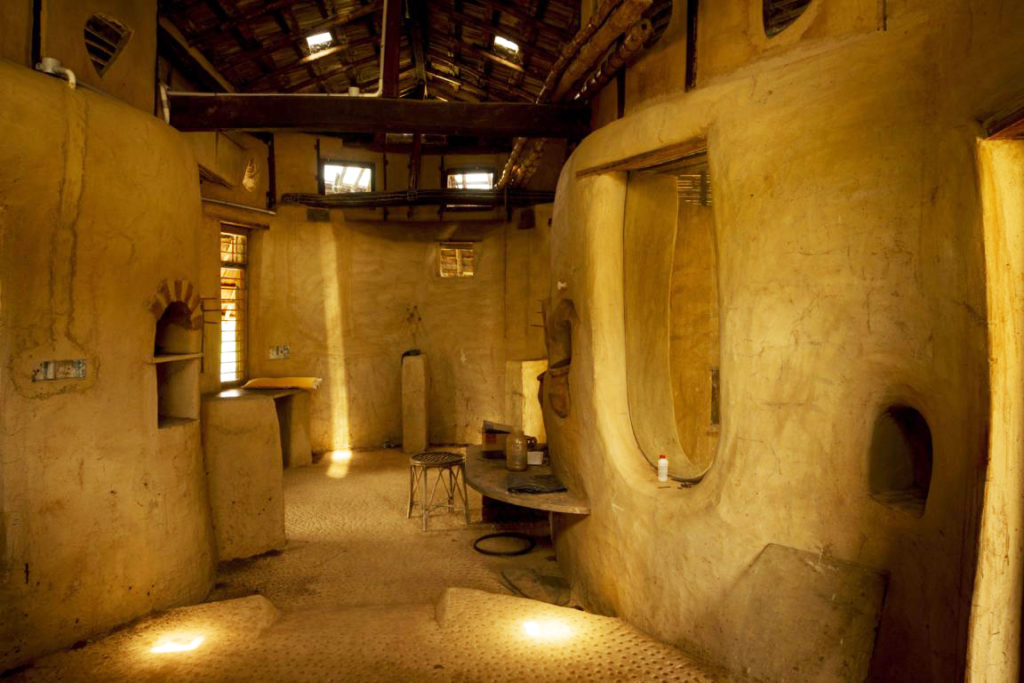
Mud walls can providing thermal comfort inside the house because they tend to moderate fluctuations of temperature.“Mud buildings are similar to the human body. Mud walls, being porous, can breathe, like our skin. This helps in maintaining comfortable indoor temperature, irrespective of extreme weather conditions outside. So one can save a lot of money spent on ACs and other mechanical means to keep the space comfortable,” says Biju Bhaskar, co-founder of Thannal Hand Sculpted Homes.
3. Recyclable
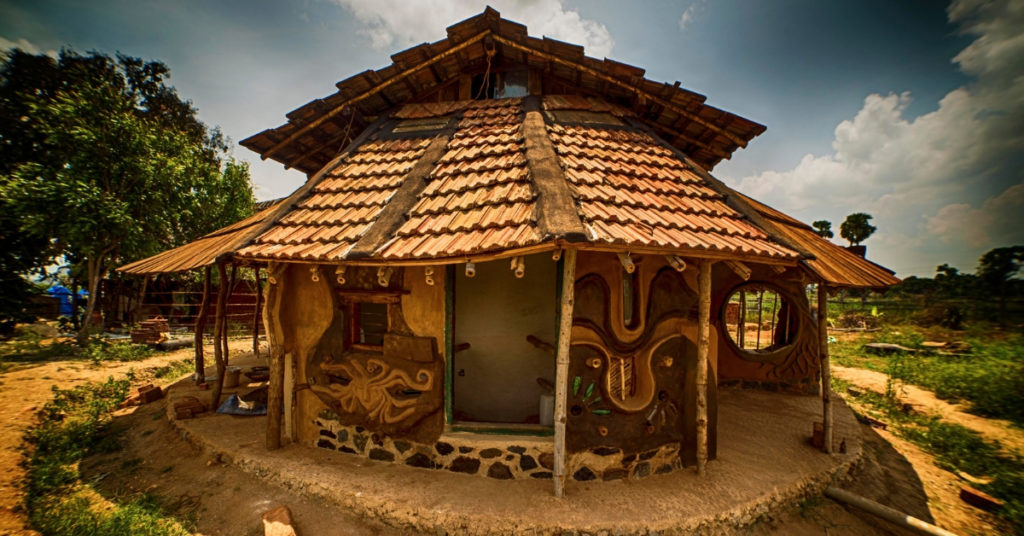
When dismantled, mud houses are recyclable or re-usable. “The material is re-usable, and if you break it down, mud can easily go back to nature. So if your son needs to build a house, he can re-use the entire material and not look for anything new. This way, we can reduce the dependency for construction from nature,” says Biju.
4. Biodegradable
Mud is an excellent example of a circular economy, where It easily goes back to nature.
5. Cost-Effective

Due to its abundance, mud or rammed earth can be procured at reasonable rates. Besides, it is a locally available material that reduces or mitigates transportation costs. This cuts down the overall construction cost up to 30%.
6. Versatility
There are four basic construction techniques to build a mud house that depend on climatic conditions, location, and its size.
- Cob: A mixture of soil, clay, cow dung and urine, straw, and lime is kneaded with tools, hands, or feet to make lumps that eventually form the walls.
- Adobe: Sun-dry clay/sand soil to form bricks.
- Wattle and Daub: Wooden/bamboo strips called wattle are ‘daubed’ with a sticky material made from mud, clay, sand, etc.
- Rammed earth: Ramming a mixture of sand, gravel and clay until it becomes rock solid.
7. Carbon Footprint
“If the cement industry were a country, it would be the third-largest carbon dioxide emitter in the world with up to 2.8bn tonnes, surpassed only by China and the US,” reads a report by Chatham House. In comparison, mud has negligible carbon footprints as it is recyclable and can be excavated from the earth. Plus, it is sourced locally, eliminating transportation (from quarry to construction sites) that otherwise would have left carbon emissions.
You can read the original article at www.thebetterindia.com
Nice, I’d love to see some modern open source plans for a manual CEB press (something equivalent to the Mardini MB-2 or TARA Balram-MI) that we can have machined and welded locally in Kerala, India.
It is always a good thing to remember why I love to use these materials so much.